Manufacturers Embrace MSPs for Proactive Cybersecurity in 2025
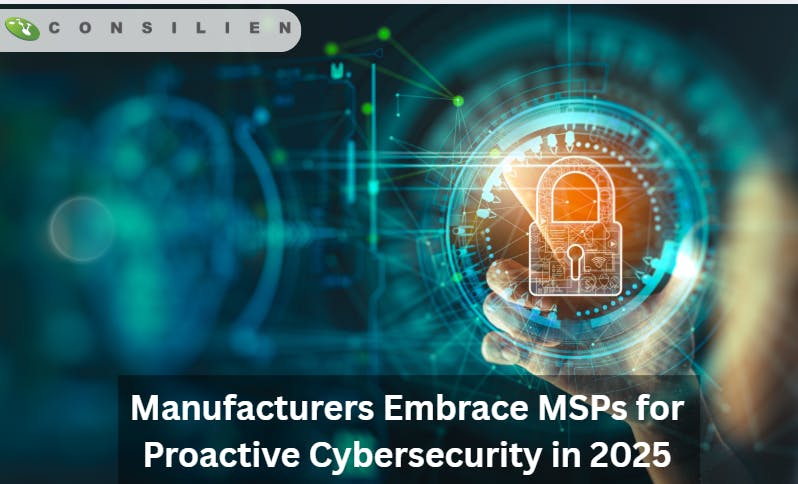
Many manufacturers still rely on a break fix model for IT. This means they only call for help when something breaks like a server crash, a network failure, or a security breach. While this may seem cost effective at first, it often leads to more problems over time. In a reactive system, problems are only fixed after they cause damage. This delay can mean hours or days of downtime, lost production, and missed delivery deadlines. Worse, security threats may go unnoticed until it’s too late. A break-fix model might have worked a decade ago, but manufacturing IT today is more connected, complex, and exposed to cyber threats. Waiting until something goes wrong before responding is now a major business risk.
Problems in Break/Fix Setups
Break/fix setups come with several issues:
- No ongoing monitoring: IT systems are not watched regularly. You find out about issues only when they disrupt operations.
- No planning: There’s little to no long-term planning for upgrades, cybersecurity, or future growth.
- Increased costs: Emergency repairs and rushed solutions often cost more than steady maintenance.
- Inconsistent support: You might work with different technicians each time, with no clear strategy or understanding of your business needs.
Most importantly, this model doesn’t help prevent problems, it only reacts to them. For manufacturers who rely on constant uptime, this is a serious weakness.
The Cost of Reactivity
Being reactive in IT management can cost manufacturers more than just money. The real damage shows up in three key areas
1. Higher Operating Costs
Every system failure costs more to fix under pressure. You may also need to pay overtime, replace hardware quickly, or hire emergency support. These costs add up.
2. Lost Productivity and Downtime
When machines can’t talk to your network, or when your systems are down, work stops. Production slows. Orders are delayed. Customers wait longer. In industries with thin margins, this kind of delay hurts your bottom line.
3. Reputation Damage and Compliance Risks
A cyberattack or data breach doesn’t just cause downtime. It can damage your reputation with partners and clients. It can also expose you to legal and regulatory issues, especially if your data protection policies are weak.
OT Specific Example
Imagine a CNC machine goes offline because of a ransomware attack. It was connected to your network, but no one noticed the outdated software. A proactive system would have flagged the weakness and patched it. But under break fix, it goes unchecked. Production halts for two days. You miss a major deadline. And now, your client is looking at other suppliers.
This is the cost of being reactive.
Proactive MSP Capabilities
Managed Service Providers (MSPs) offer an alternative, a proactive model that focuses on preventing problems before they happen.
Here’s what smart manufacturers get with a proactive MSP.
1. 24/7 Monitoring and Threat Detection
A good MSP constantly watches your systems. If anything looks unusual like suspicious traffic or a system slowing down they take action before it causes real harm.
2. Regular Patching and Software Updates
Outdated software is one of the top reasons cybercriminals break into manufacturing networks. MSPs handle patching and updates automatically, so your systems stay secure.
3. Backup and Disaster Recovery
If something ever does go wrong, a proactive MSP ensures your data is backed up and systems can be restored quickly, with minimal downtime.
4. Network Management and Maintenance
MSPs make sure your routers, firewalls, and devices are set up correctly and running smoothly. This reduces connection problems and keeps operations flowing.
5. Strategic vCIO Planning
Many MSPs offer virtual Chief Information Officer (vCIO) services. A vCIO works with you to build a roadmap for your IT. This includes planning upgrades, improving security, and making sure your IT supports your business goals.
Real World ROI. What Manufacturers Are Seeing
When manufacturers switch to a proactive MSP, they often see real, measurable improvements.
Example- Reduced Downtime
One manufacturer who partnered with a proactive MSP reduced their system downtime by 65% in the first year. That meant more time on the production floor and fewer delays.
Example- Lower IT Costs
With regular maintenance, issues are caught early. This leads to fewer emergencies and fewer expensive repairs. In many cases, manufacturers report saving up to 25% on their yearly IT costs.
Example- Stronger Cybersecurity
An MSP set up ongoing vulnerability scans for a plant. Within 3 months, they found and patched 12 weak points including outdated software on equipment that had direct internet access. These are just a few ways manufacturers benefit from shifting to proactive IT support.
Signs Your MSP Is Reactive vs Proactive
Not all MSPs work the same way. Some still follow a mostly reactive model, even if they call themselves “managed.” Use this checklist to see where your provider stands:
If most boxes in the “Reactive” column are checked, it might be time to switch to a more proactive partner.
Future Ready Manufacturers Go Proactive
Manufacturers that still rely on break/fix IT support are taking a risk they can’t afford in 2025. As networks grow and cyber threats increase, waiting for something to go wrong is no longer a smart choice. At Consilien IT Company, we don’t wait for problems to happen we work to stop them before they start. Our cybersecurity-focused MSP services are built for manufacturing environments, where every minute of uptime matters. Ready to take control of your IT future? Speak with a Consilien IT Company vCIO to build a roadmap that fits your business, supports your growth, and keeps your systems secure without the guesswork.