HOW AI ENHANCES IOT PREDICTIVE MAINTENANCE
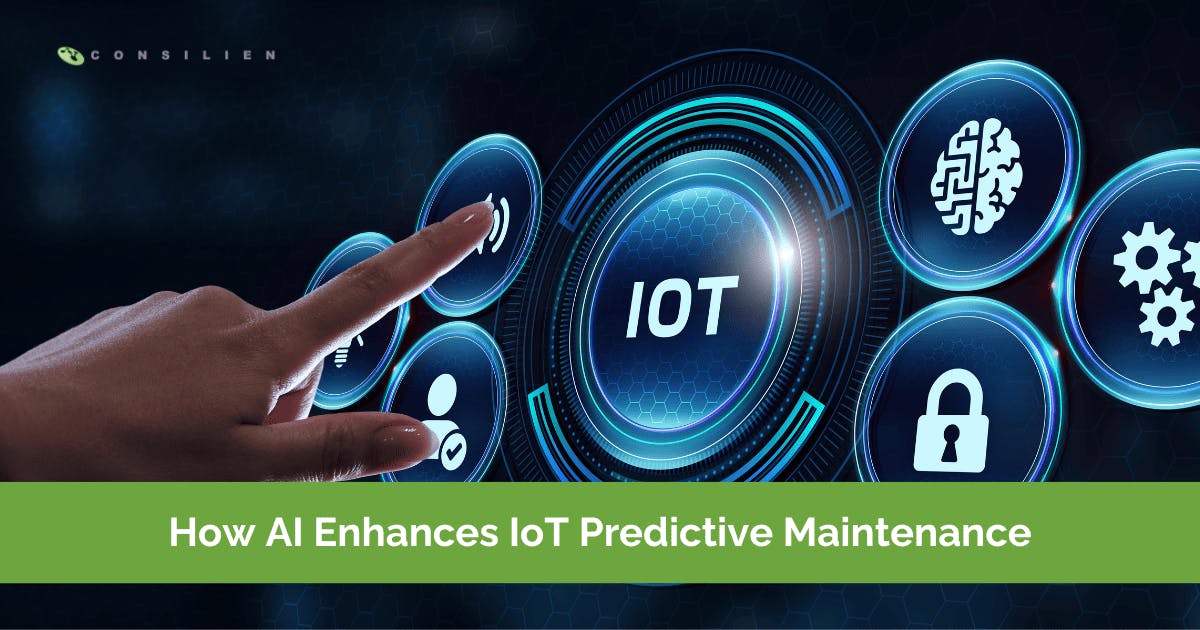
Predictive maintenance has become a cornerstone of operational efficiency across industries. By combining IoT’s real-time data collection capabilities with AI’s analytical power, businesses can stay ahead of costly equipment failures. But the journey to effective predictive maintenance isn’t just about the technology—it’s about how you integrate these tools into your processes to maximize their impact.
At Consilien, we’ve spent decades helping businesses optimize their IT infrastructure, and the benefits of predictive maintenance are clear: reduced downtime, improved efficiency, and significant cost savings. Here’s how AI enhances IoT predictive maintenance and how you can leverage this powerful combination to stay competitive.
What Is Predictive Maintenance?
Predictive maintenance uses data to anticipate and prevent equipment failures before they happen. Unlike reactive maintenance (fix it when it breaks) or preventive maintenance (scheduled upkeep), predictive maintenance leverages IoT sensors to collect data and AI algorithms to analyze it for warning signs of potential issues.
By monitoring equipment in real time, businesses can make smarter decisions, reduce unexpected downtime, and extend the lifespan of their assets.
The Role of IoT in Predictive Maintenance
IoT (Internet of Things) sensors are the backbone of predictive maintenance. These sensors continuously monitor equipment, tracking metrics like temperature, vibration, and pressure. This real-time data creates a foundation for AI algorithms to work their magic.
For example, in manufacturing, IoT sensors can monitor machinery 24/7, identifying subtle shifts in performance that humans might miss. This granular data is invaluable for predicting failures before they disrupt operations.
How AI Enhances Predictive Maintenance?
While IoT provides the raw data, AI transforms it into actionable insights. Here’s how AI takes predictive maintenance to the next level:
- Pattern Recognition: AI identifies patterns in equipment performance, flagging anomalies that could indicate potential issues.
- Failure Prediction: Using machine learning models, AI predicts the likelihood and timing of failures, enabling proactive repairs.
- Prescriptive Analytics: Beyond predicting issues, AI suggests the best course of action to mitigate risks.
According to Deloitte, organizations that integrate AI into their IoT predictive maintenance strategies report a 40% improvement in operational efficiency.
Benefits of AI-Enhanced Predictive Maintenance
The advantages of combining AI and IoT in predictive maintenance are transformative:
- Reduced Downtime: Unplanned downtime costs businesses an average of $84,000 per hour (Veeam). Predictive maintenance minimizes these disruptions.
- Cost Savings: Businesses save up to 30% on maintenance costs with proactive strategies (Flexera).
- Improved Safety: AI detects issues before they lead to dangerous malfunctions.
- Enhanced Efficiency: Optimized maintenance schedules mean fewer interruptions and more productive operations.
Challenges in Implementing AI and IoT for Predictive Maintenance
While the benefits are clear, implementing AI and IoT predictive maintenance comes with challenges:
- Data Overload: IoT sensors generate massive amounts of data. Filtering out noise and focusing on actionable insights is key.
- Integration with Legacy Systems: Many organizations struggle to integrate new technology with outdated infrastructure.
- Skill Gaps: Effective implementation requires expertise in AI, IoT, and data analysis.
Industries Leading the Way
Predictive maintenance is already transforming industries:
- Manufacturing: Smart factories use IoT and AI to monitor equipment in real time, reducing downtime by up to 50%.
- Healthcare: Hospitals leverage IoT sensors to monitor critical equipment like ventilators, ensuring reliability.
- Transportation: Fleet operators use AI to predict vehicle maintenance needs, reducing breakdowns and operational costs.
Steps to Implement AI and IoT for Predictive Maintenance
If you’re ready to adopt predictive maintenance, follow these steps:
- Evaluate Infrastructure: Identify areas where IoT sensors can provide the most value.
- Select Tools: Choose IoT devices and AI platforms that fit your needs.
- Start Small: Begin with a pilot project to test effectiveness.
- Scale Gradually: Expand implementation across your operations.
- Monitor and Optimize: Continuously refine processes based on results.
The Future of AI and IoT in Predictive Maintenance
The predictive maintenance landscape is evolving rapidly. Trends to watch include:
- AI at the Edge: Processing data closer to IoT devices for faster insights.
- Deeper Integration with Cloud Computing: Leveraging cloud platforms for scalability.
- Autonomous Maintenance Systems: AI-driven systems that predict and act without human intervention.
According to Precedence Research, the global predictive maintenance market is projected to reach $79.70 billion by 2034.
Conclusion
AI-enhanced IoT predictive maintenance isn’t just about technology—it’s about transforming how businesses operate. By proactively addressing issues, organizations can reduce downtime, save costs, and improve safety. As predictive maintenance continues to evolve, it’s clear that businesses that invest in these solutions today will be the leaders of tomorrow.
Ready to optimize your IT infrastructure and embrace smarter solutions? Reach out to our team today!
References:
1) Predictive Maintenance Market Growth: The global predictive maintenance market size was valued at USD 7.85 billion in 2022 and is expected to grow at a compound annual growth rate (CAGR) of 29.5% from 2023 to 2030. Grand View Research
2) Unplanned Downtime Costs: Unplanned downtime in manufacturing can cost a company as much as $260,000 an hour. IIoT World
3) Operational Efficiency Improvement with AI Integration: Integrating AI and ML into predictive maintenance prevents unplanned downtime and asset failures. Grand View Research
4) Cost Savings with Predictive Maintenance: The cost of an hour’s downtime in an automotive plant is now more than $2 million – up from $1.3 million in 2019–20. Siemens Assets
5) Market Projection for Predictive Maintenance: The global predictive maintenance market is anticipated to reach around USD 32.30 billion by 2030, growing at a CAGR of 27.4% between 2024 and 2030. NextMSC